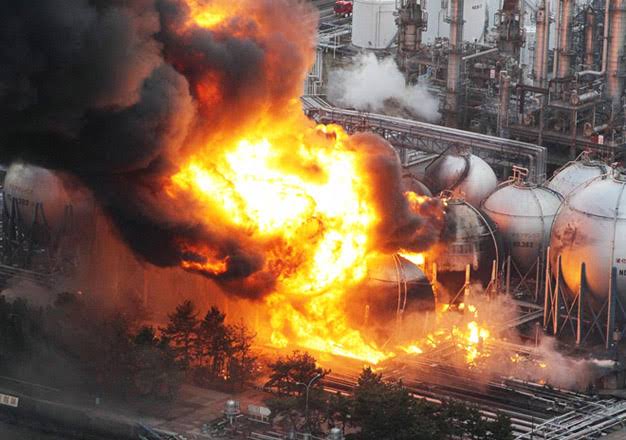
Preventing Fire Hazard In The Oil & Gas Industry
Date posted: 24, June 2021In the complex industry of oil and gas, there’s a lot that could go wrong. One of the more serious risks for this industry is the potential for fires and explosions. Major causes of accidents include human errors, mechanical failure, natural causes, and deficient procedures and training when dealing with emergency situations.
According to Occupational Safety and Health Administration (OSHA), between 2005 and 2015, there were 85 fire-related deaths in the oil and gas industry. So, how can you prevent fire outbreaks in your company and protect your employees?
First, let us take a look at the major causes of fire outbreaks in the oil and gas industry.
Hot-works
Hot work includes welding, cutting, burning, abrasive blasting, and other heat-producing operations. This type of work generates hot sparks and slag. Those can then come into contact with nearby combustibles and flammable gases. Hot work presents an increased risk of fire and explosion hazards because it is most often performed in confined and enclosed spaces.
Accidents may occur during hot work due to the structure of vessels, where hot work in space can cause fire or explosion in an adjacent space that has not been evaluated safe for hot work.
Ignition of flammable vapors
Liquids (such as petrol and other fuels) and solvents in industrial products (such as paint, ink, adhesives, and cleaning fluids) give off flammable vapor which, when mixed with air, can ignite or explode. Vehicles and motorized equipment present ignition hazards when located near flammable vapor sources.
Using wrong materials in corrosion control The effect of corrosion in the oil industry leads to the failure of parts. This failure results in shutting down the plant to clean the facility. In other to take away this corrosion, wrong materials such as metallic tools are deployed to carry out this activity. This results in a spark that can cause an inferno in the facility, destroying life and properties.
Prevention
Using hot-work permit: A hot work permit allows employers to maintain safety and control over potentially hazardous hot work operations. The hot work permit system reinforces to workers the safety requirements of their work situation. Under the hot work permit system, a firewatcher is required to oversee a hot work site for at least 30 minutes after the completion of the job.
Conduct fire risk assessment
Fire Risk Assessments are a great way to ensure that safe work practices are being followed. They will help you to confirm if the risk of fire has been minimized. A risk assessment should be carried out by someone who has had sufficient training and has good experience and/or knowledge of fire safety.
Having fire extinguishers close
Employees should always know where to find the nearest fire extinguisher. This is even more critical when performing hot work. Hoses and other suppression equipment can work too.
Conductivity
Corrosion will not occur in distilled water and the rate of corrosion will increase as the conductivity increases due to the presence of more ions in the solution. The corrosion rate of steel reaches a maximum close to the normal ionic content of seawater.
Wearing proper PPE
According to the OSHA eTools, clothing made from 100% cotton or wool may be acceptable if its weight is appropriate for the flame and electric arc conditions to which a worker could be exposed. As heat levels increase, these materials will not melt, but they can ignite and continue to burn. It is the responsibility of the employer to provide this to the employee.
Use non-metallic tools for corrosion control
Fortunately, wrong materials are sometimes deployed to carry out corrosion control. This results in a spark that can cause an inferno in the facility, destroying life and properties. For effective corrosion control, and safety of facility and personnel, use Nipplestar 100% non-spark tools and pneumatic machines. Made of brass, copper, and aluminum alloy to guarantee zero sparks. Hence, saving you production downtime and heavy investment in corrosion control campaigns. As it can be used to attack developing corrosion during your production time and work against such corrosion expansion in your facility.